- Wyciskanie hantlami na ławce płaskiej – technika, błędy i korzyści
- Jak często ćwiczyć jogę? Przewodnik po praktyce i celach
- Joga czakralna – jak harmonizować energię ciała i umysłu?
- Ćwiczenia z gumą oporową dla mężczyzn – odkryj skuteczność treningu w domu
- Plan treningowy dla początkujących i średniozaawansowanych pływaków
Jak wybrać idealne uszczelnienia hydrauliczne do Twojego projektu?
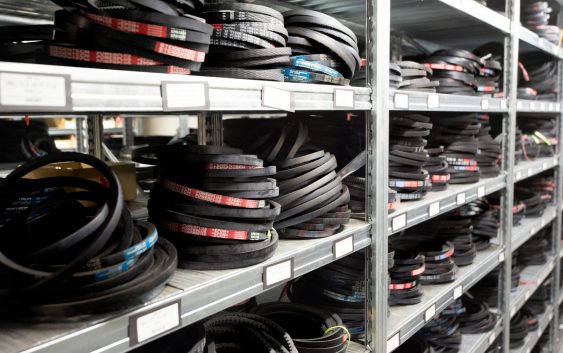
Uszczelnienia hydrauliczne to kluczowe elementy w wielu systemach hydraulicznych, które odgrywają istotną rolę w zapewnieniu ich prawidłowego funkcjonowania. Dzięki nim możliwe jest skuteczne zapobieganie wyciekom płynów, co nie tylko zwiększa efektywność, ale także chroni przed kosztownymi awariami. W obliczu rosnącej złożoności nowoczesnych maszyn i pojazdów, zrozumienie różnych rodzajów uszczelnień oraz materiałów, z których są wykonane, staje się niezwykle istotne. Wybór odpowiedniego uszczelnienia wymaga przemyślanej analizy, ponieważ niewłaściwe decyzje mogą prowadzić do poważnych konsekwencji. Jakie są kluczowe aspekty, które należy wziąć pod uwagę przy ich doborze?
Czym są uszczelnienia hydrauliczne?
Uszczelnienia hydrauliczne odgrywają kluczową rolę w systemach hydraulicznych, a ich znaczenie trudno przecenić. Głównym celem tych elementów jest zapobieganie wyciekom płynów oraz zapewnienie szczelności połączeń. Działają jak bariera między różnymi częściami układu, co umożliwia skuteczne przekazywanie ciśnienia. Można je znaleźć w wielu zastosowaniach, takich jak:
- maszyny przemysłowe,
- pojazdy,
- różnorodne urządzenia hydrauliczne.
Projekty uszczelniaczy hydraulicznych mają ogromne znaczenie dla prawidłowego funkcjonowania siłowników. Dzięki nim udaje się uniknąć wycieków substancji roboczych, zwłaszcza oleju. Odpowiednio dobrane uszczelnienia pozwalają siłownikom na pracę w sposób efektywny i niezawodny. Warto zauważyć, że dostępnych jest wiele typów uszczelnień hydraulicznych, co daje możliwość ich idealnego dopasowania do konkretnych warunków eksploatacji.
Aby układy hydrauliczne działały niezawodnie, konieczne jest stosowanie odpowiednich uszczelnień. Problemy mogą się pojawić na skutek:
- błędnej konstrukcji urządzeń,
- niewłaściwego montażu,
- złego doboru materiałów.
Niezwykle istotna jest również właściwa eksploatacja tych elementów. Dlatego regularne przeprowadzanie diagnostyk i konserwacji uszczelnień hydraulicznych ma kluczowe znaczenie – pozwala to zminimalizować straty produkcyjne wynikające z ewentualnych awarii.
Jakie są rodzaje uszczelnień hydraulicznych?
Uszczelnienia hydrauliczne można klasyfikować w kilka kluczowych kategorii, które są niezbędne do zapobiegania wyciekom oraz zapewnienia sprawnego działania układów hydraulicznych. Oto najważniejsze z nich:
- Uszczelniacze statyczne wykorzystuje się tam, gdzie nie ma ruchu między elementami,
- w tej grupie znajdują się połączenia gwintowe i różnego rodzaju części konstrukcyjne,
- do najczęściej stosowanych należą uszczelki płaskie oraz O-ringi.
- Uszczelniacze dynamiczne pracują w warunkach ruchu, na przykład w siłownikach hydraulicznych czy pompach,
- w tej kategorii wyróżniają się uszczelnienia tłoczyskowe i obrotowe,
- muszą sprostać różnorodnym obciążeniom i zmianom ciśnienia.
- Uszczelniacze wielostrumieniowe przeznaczone są do sytuacji wymagających utrzymania szczelności przy jednoczesnym przepływie wielu mediów hydraulicznych,
- często znajdują zastosowanie w bardziej skomplikowanych systemach hydraulicznych.
Każdy typ uszczelnienia ma swoje unikalne cechy oraz zastosowania dostosowane do konkretnych warunków pracy. Właściwy wybór uszczelnienia jest kluczowy dla efektywności całego systemu hydraulicznego.
Uszczelniacze statyczne
Uszczelniacze statyczne odgrywają niezwykle ważną rolę w hydraulice, szczególnie tam, gdzie elementy pozostają w stałej pozycji. Ich głównym celem jest zapobieganie wyciekom płynów w miejscach, które nie ulegają ruchom, takich jak flansze czy różnego rodzaju złącza.
W przeciwieństwie do uszczelniaczy dynamicznych, które muszą radzić sobie z ruchem i zmieniającymi się warunkami, uszczelniacze statyczne są projektowane z myślą o długotrwałej szczelności. Wśród najpopularniejszych typów tych uszczelnień znajdują się zarówno:
- uszczelki płaskie,
- o-ringi.
W kontekście zastosowań hydraulicznych kluczowe jest odpowiednie dobranie uszczelnienia do specyfiki danego projektu. Wysokiej jakości materiały oraz precyzyjne dopasowanie mogą znacząco poprawić efektywność systemu i zmniejszyć ryzyko awarii spowodowanych wyciekami. Dodatkowo, właściwe uszczelnienie przyczynia się do zwiększenia trwałości całego układu hydraulicznego.
Uszczelniacze dynamiczne
Uszczelniacze dynamiczne pełnią niezwykle ważną funkcję w systemach hydraulicznych. Ich konstrukcja jest przemyślana tak, aby mogły efektywnie pracować w ruchu, co wiąże się z koniecznością dostosowania do zmieniających się warunków, takich jak ciśnienie i prędkość. W odróżnieniu od uszczelnień statycznych, które pozostają w jednym miejscu, uszczelniacze dynamiczne muszą stawiać czoła tarciu oraz różnorodnym wyzwaniom związanym z ich użytkowaniem.
Te elementy są szeroko stosowane nie tylko w cylindrach hydraulicznych, ale także w różnych urządzeniach mechanicznych. Na przykład, znajdują swoje miejsce w:
- silnikach hydraulicznych,
- pompach,
- maszynach budowlanych,
- systemach chłodzenia,
- układach napędowych.
Odpowiednio dobrany uszczelniacz dynamiczny znacząco podnosi efektywność systemów hydraulicznych i skutecznie zapobiega wyciekom płynów roboczych.
Podczas wyboru uszczelniaczy dynamicznych kluczowe jest uwzględnienie specyfikacji technicznych projektu oraz warunków chemicznych i temperaturowych pracy. Dobrze zaprojektowane i starannie wykonane uszczelniacze mają potencjał znacznie wydłużyć żywotność poszczególnych komponentów systemu hydraulicznego.
Uszczelniacze wielostrumieniowe
Uszczelniacze wielostrumieniowe pełnią niezwykle istotną funkcję w systemach hydraulicznych, które kontrolują przepływ płynów przez liczne kanały. Ich starannie przemyślana budowa gwarantuje efektywną szczelność nawet w najbardziej skomplikowanych układach. To z kolei jest kluczowe dla prawidłowego funkcjonowania maszyn i urządzeń hydraulicznych.
Te elementy znajdują zastosowanie w wielu sektorach, takich jak:
- przemysł maszynowy,
- przemysł energetyczny,
- budownictwo,
- transport,
- automatyka przemysłowa.
Dzięki nim możliwe jest skuteczne uszczelnienie, co przekłada się na:
- poprawę wydajności całego systemu,
- redukcję ryzyka niepożądanych wycieków.
Dlatego też właściwy wybór uszczelniaczy wielostrumieniowych ma fundamentalne znaczenie dla optymalnej pracy hydrauliki. Zrozumienie specyfiki działania tych uszczelniaczy oraz warunków, w jakich będą eksploatowane, jest równie ważne. Muszą być one precyzyjnie dostosowane do:
- ciśnienia roboczego,
- temperatury,
- rodzaju płynu.
Aby mogły niezawodnie spełniać swoje zadania przez długi czas bez ryzyka awarii.
Jakie materiały są używane do produkcji uszczelnień hydraulicznych?
Uszczelnienia hydrauliczne mają niezwykle istotne znaczenie w funkcjonowaniu systemów hydraulicznych. Wybór materiałów, z których są wykonane, bezpośrednio wpływa na ich efektywność oraz niezawodność. Wśród najczęściej stosowanych surowców można wymienić:
- gumę,
- PTFE (teflon),
- metale.
Guma cieszy się dużą popularnością ze względu na swoją elastyczność i odporność na działanie różnych substancji chemicznych. Uszczelki wykonane z tego materiału doskonale sprawdzają się w zmieniających się warunkach ciśnienia i temperatury, co czyni je idealnym wyborem do szerokiego zakresu zastosowań hydraulicznych.
PTFE, znany powszechnie jako teflon, charakteryzuje się znakomitą odpornością zarówno na działanie chemikaliów, jak i ekstremalne temperatury. Te wyjątkowe właściwości sprawiają, że jest często wykorzystywany w aplikacjach wymagających wysokiej odporności na ścieranie oraz w trudnych warunkach eksploatacyjnych.
Metale takie jak stal hartowana czy węglik krzemu znajdują zastosowanie głównie w uszczelnieniach mechanicznych. Oferują one nie tylko świetną wytrzymałość mechaniczną, ale także dużą odporność na zużycie, co jest kluczowe przy pracy pod wysokim ciśnieniem.
Podczas wyboru materiałów do produkcji uszczelnień hydraulicznych warto zwrócić uwagę na specyfikę danego zastosowania oraz wymagania związane z temperaturą i ciśnieniem roboczym.
Guma
Guma to jeden z najpopularniejszych materiałów stosowanych w produkcji uszczelnień hydraulicznych. Jej elastyczność sprawia, że doskonale nadaje się do tworzenia uszczelniaczy statycznych, które odgrywają kluczową rolę w wielu systemach hydraulicznych. Dodatkowo, guma charakteryzuje się wysoką odpornością na różnorodne chemikalia, co czyni ją idealnym wyborem w trudnych warunkach pracy.
W kontekście uszczelnień hydraulicznych, guma często łączy się z innymi materiałami, co znacząco podnosi jej właściwości użytkowe. Ze względu na swoją wszechstronność oraz dostępność, inżynierowie chętnie korzystają z gumy przy projektowaniu systemów hydraulicznych. Wybór tego materiału zapewnia efektywność oraz niezawodność całego układu.
Ponadto, odpowiedni dobór rodzaju gumy – jak na przykład elastomery – może mieć istotny wpływ na wydajność uszczelnień w różnych warunkach ciśnienia i temperatury. Kluczowe jest również zwrócenie uwagi na specyfikacje techniczne gumy, aby uniknąć ewentualnych problemów związanych z jej zastosowaniem w konkretnych aplikacjach hydraulicznych.
PTFE (teflon)
Uszczelnienia hydrauliczne wykonane z PTFE, znanego powszechnie jako teflon, cieszą się dużym uznaniem dzięki swoim niezwykłym właściwościom. Politetrafluoroetylen wyróżnia się nie tylko wysoką odpornością chemiczną, ale także termiczną, co sprawia, że jest doskonałym wyborem w wymagających warunkach.
Teflonowe uszczelki sprawdzają się znakomicie w systemach o podwyższonym ciśnieniu oraz temperaturze. Dzięki swojej odporności na różnorodne substancje chemiczne znajdują zastosowanie w wielu sektorach, takich jak:
- przemysł,
- branża spożywcza,
- sektor chemiczny.
Co więcej, ich właściwości antyadhezyjne znacząco ograniczają ryzyko przywierania do innych materiałów.
Dodatkowo uszczelnienia hydrauliczne z PTFE są łatwe do zamontowania i utrzymania. Charakteryzują się:
- długowiecznością,
- stabilnością wymiarową,
- odpornością na ekstremalne warunki pracy.
To sprawia, że stanowią nie tylko skuteczne rozwiązanie techniczne, ale również ekonomiczne – wymagają bowiem mniejszych nakładów na konserwację i mogą służyć przez dłuższy czas.
W kontekście uszczelnień hydraulicznych PTFE to niezastąpiony materiał dla aplikacji potrzebujących wysokiej wydajności oraz niezawodności przez długi okres użytkowania.
Metal
Uszczelnienia metalowe pełnią niezwykle istotną funkcję w systemach hydraulicznych, zwłaszcza w miejscach, gdzie kluczowa jest wysoka wytrzymałość oraz odporność na znaczne ciśnienia. W przeciwieństwie do innych materiałów, metalowe uszczelnienia oferują lepszą trwałość i niezawodność, co czyni je doskonałym rozwiązaniem nawet w najbardziej wymagających warunkach pracy.
Chętnie wykorzystuje się je w połączeniach, gdzie inne materiały mogłyby zawieść. Metalowe uszczelnienia powstają przy użyciu różnych technik produkcji, takich jak:
- formowanie,
- spawanie.
Te procesy pozwalają im osiągnąć odpowiednią szczelność oraz odporność na ekstremalne warunki. Ich unikalne właściwości sprawiają, że są one niezbędnym elementem wielu branż, w tym przemysłu motoryzacyjnego oraz energetycznego.
Dokonując wyboru odpowiedniego metalowego uszczelnienia hydraulicznego, można znacząco wpłynąć na efektywność całego systemu. Dobrze dobrane uszczelnienie nie tylko minimalizuje ryzyko wycieków, ale również zwiększa żywotność komponentów.
Jakie są kluczowe czynniki przy wyborze uszczelnień hydraulicznych?
Wybór odpowiednich uszczelnień hydraulicznych jest niezwykle istotny dla sprawnego funkcjonowania systemów hydraulicznych. Przy podejmowaniu decyzji warto rozważyć kilka kluczowych aspektów:
- ciśnienie robocze – uszczelnienia muszą być dobrane do określonego zakresu ciśnień, aby zapewnić szczelność i zminimalizować ryzyko wycieków,
- temperatura pracy – ekstremalne warunki mogą znacząco wpłynąć na właściwości materiałów uszczelniających, dlatego konieczne jest wybieranie uszczelnień odpornych na zmiany termiczne,
- środowisko chemiczne – różnorodność mediów roboczych wymaga stosowania materiałów odpornych na korozję oraz działanie chemikaliów.
Odpowiedni dobór tych materiałów ma kluczowe znaczenie dla trwałości i niezawodności całego systemu.
Ciśnienie robocze
Ciśnienie robocze odgrywa kluczową rolę przy selekcji uszczelnień hydraulicznych. Właściwie dobrane uszczelnienia muszą wytrzymać maksymalne ciśnienie występujące w systemie, co jest niezbędne dla ich efektywności i długowieczności. Niewłaściwy dobór może skutkować poważnymi problemami, takimi jak:
- awarie,
- wycieki,
- szybsze zużycie innych komponentów.
W przypadku uszczelnień hydraulicznych istotne jest również zwrócenie uwagi na materiały oraz konstrukcję uszczelniaczy. Różne materiały mają różną odporność na wysokie ciśnienia, co sprawia, że przed podjęciem decyzji warto dokładnie zrozumieć specyfikę ciśnienia roboczego danego systemu oraz zapoznać się z technicznymi parametrami proponowanych rozwiązań.
Dzięki starannemu doborowi uszczelnień hydraulicznych można znacząco zwiększyć efektywność całego układu. Co więcej, pozwoli to uniknąć kosztownych napraw, które mogą wyniknąć z nieodpowiedniego dopasowania elementów.
Temperatura pracy
Temperatura pracy odgrywa kluczową rolę w doborze uszczelnień hydraulicznych. Różne materiały, z jakich są one wykonane, różnią się pod względem zakresów temperatur, w których mogą działać efektywnie.
Na przykład:
- guma sprawdza się w przedziale od -40 do 100 stopni Celsjusza,
- PTFE, znany jako teflon, jest w stanie wytrzymać dużo wyższe temperatury – nawet do 260 stopni Celsjusza,
- metalowe uszczelnienia także wyróżniają się wysoką odpornością na ekstremalne warunki cieplne.
Aby zapewnić skuteczność systemów hydraulicznych, ważne jest odpowiednie dopasowanie materiału do przewidywanej temperatury pracy. To nie tylko zwiększa wydajność, ale również minimalizuje ryzyko awarii i wycieków. Przy wyborze uszczelnień warto również zwrócić uwagę na inne aspekty, takie jak ciśnienie robocze czy środowisko chemiczne, co pozwala na osiągnięcie najlepszej efektywności całego systemu.
Środowisko chemiczne
Środowisko chemiczne, w którym funkcjonują uszczelnienia hydrauliczne, odgrywa kluczową rolę w ich trwałości oraz wydajności. Właściwy dobór materiałów jest niezwykle istotny, aby zapewnić odporność na substancje chemiczne obecne w danym systemie.
Przy wyborze uszczelnień hydraulicznych warto rozważyć różnorodne czynniki chemiczne, takie jak:
- pH medium,
- temperatura,
- ciśnienie robocze.
Materiały muszą być starannie dostosowane do specyficznych warunków. Na przykład guma może nie wytrzymać działania silnych kwasów czy zasad, podczas gdy PTFE (teflon) wykazuje lepszą odporność na wiele różnych chemikaliów.
Co więcej, dla utrzymania wysokiej efektywności systemów hydraulicznych istotne jest monitorowanie potencjalnych reakcji między uszczelnieniami a współpracującymi z nimi substancjami. Ignorowanie właściwości chemicznych medium może skutkować przyspieszonym zużyciem lub awarią uszczelnień.
Dokładny dobór materiałów nie tylko wydłuża żywotność uszczelnień hydraulicznych, ale także podnosi poziom bezpieczeństwa i niezawodności całego systemu hydraulicznego.
Jak dobrać idealny uszczelniacz hydrauliczny do projektu?
Dobór odpowiedniego uszczelniacza hydraulicznego do projektu to proces, który wymaga przemyślanej strategii i uwagi na detale. Pierwszym krokiem jest dokładna analiza wymagań danego projektu. Niezwykle istotne jest określenie takich parametrów jak:
- ciśnienie robocze,
- temperatura pracy,
- chemiczne właściwości medium.
Te czynniki mają kluczowy wpływ na wybór najlepszego uszczelnienia hydraulicznego.
Warto również skorzystać z porad specjalistów zajmujących się dostawami uszczelnień hydraulicznych. Tacy eksperci posiadają nie tylko obszerną wiedzę, ale także praktyczne doświadczenie związane z różnorodnymi materiałami i technologiami dostępnymi na rynku. Konsultacja z nimi może przynieść cenne wskazówki dotyczące optymalnych rozwiązań dla konkretnego zastosowania.
Na zakończenie procesu niezwykle ważne jest przeprowadzenie testów i walidacji wybranych opcji. Powinny one obejmować zarówno symulacje warunków pracy, jak i rzeczywiste aplikacje, co pozwoli upewnić się, że wybrane uszczelnienia hydrauliczne spełniają wszystkie stawiane im wymagania projektowe. Tylko wieloaspektowe podejście do tych trzech etapów zapewni długotrwałą skuteczność oraz niezawodność systemu hydraulicznego.
Analiza wymagań projektu
Analiza wymagań projektu to niezwykle istotny krok w wyborze odpowiedniego uszczelniacza hydraulicznego. W tym procesie kluczowe jest uwzględnienie różnorodnych parametrów technicznych i operacyjnych, takich jak:
- ciśnienie robocze,
- temperatura pracy,
- środowisko chemiczne.
Pierwszym krokiem analizy jest określenie specyfikacji dla uszczelnienia hydraulicznego. Należy zrozumieć warunki, w jakich będzie ono funkcjonować oraz jakie obciążenia musi znieść. Również istotne są wymagania dotyczące trwałości i niezawodności tego elementu.
Następnie warto ocenić dostępne materiały, które mają wpływ na efektywność uszczelnienia. Odpowiedni dobór materiału może znacząco podnieść wydajność całego systemu hydraulicznego. Przykładowo, zwrócenie uwagi na:
- kompatybilność materiałów z cieczą roboczą,
- odporność na czynniki chemiczne.
Na zakończenie analiza wymagań projektu powinna obejmować również konsultacje z dostawcami technologii uszczelnień hydraulicznych. Tego rodzaju rozmowy mogą dostarczyć cennych wskazówek dotyczących najlepszego rozwiązania dla konkretnej aplikacji, co przyczyni się do zwiększenia efektywności systemów hydraulicznych.
Konsultacja z dostawcą
Konsultacja z dostawcą uszczelnień hydraulicznych to kluczowy etap w poszukiwaniu optymalnych rozwiązań dla danego projektu. Specjalista dysponujący odpowiednią wiedzą może dostarczyć cennych informacji na temat:
- materiałów,
- konstrukcji,
- różnych typów uszczelnień.
W trakcie takiego spotkania warto poruszyć kwestie techniczne, takie jak:
- ciśnienie robocze,
- temperatura pracy.
Dzięki temu dostawca może pomóc w identyfikacji ewentualnych problemów oraz doradzić, jakie uszczelnienia będą najbardziej odpowiednie biorąc pod uwagę chemiczne środowisko ich użycia.
Współpraca z ekspertem otwiera także możliwość:
- testowania różnych rozwiązań,
- weryfikacji ich skuteczności przed rozpoczęciem produkcji.
Taka strategia nie tylko zwiększa szanse na sukces projektu, ale także minimalizuje ryzyko awarii spowodowanych niewłaściwie dobranymi uszczelnieniami hydraulicznymi.
Testowanie i walidacja
Testowanie i weryfikacja uszczelniaczy hydraulicznych to niezwykle istotne etapy, które pozwalają nam na potwierdzenie, że te produkty odpowiadają zarówno wymaganiom technicznym, jak i oczekiwaniom użytkowników.
Podczas testów wykonujemy szereg różnorodnych analiz, w tym:
- badanie ciśnienia roboczego,
- temperatury pracy,
- odporności na różne substancje chemiczne.
Takie działania są kluczowe dla oceny jakości uszczelniaczy.
Weryfikacja ma na celu ustalenie, czy dane uszczelnienia pasują do konkretnego systemu hydraulicznego. W tym kontekście często przeprowadzamy:
- symulacje warunków eksploatacyjnych,
- długoterminowe testy,
- co pozwala nam uniknąć problemów związanych z wyciekami
- oraz zwiększa efektywność całego systemu.
Również odpowiednia dokumentacja wyników testów odgrywa kluczową rolę. Gwarantuje ona przejrzystość w zakresie wyboru i zastosowania uszczelniaczy hydraulicznych. Dzięki właściwemu podejściu do testowania i walidacji budujemy fundamenty pewności co do niezawodności oraz trwałości tych elementów w różnych aplikacjach przemysłowych.
Jakie są zalety stosowania uszczelnień hydraulicznych?
Stosowanie uszczelnień hydraulicznych przynosi wiele korzyści w różnych sektorach przemysłu. Przede wszystkim, te elementy znacznie zwiększają efektywność systemów hydraulicznych, co jest kluczowe dla optymalizacji działania maszyn i urządzeń. Dzięki nim można osiągnąć lepsze ciśnienie robocze oraz wyższą wydajność całego systemu.
Inną istotną zaletą jest ich rola w ochronie przed wyciekami. Odpowiednio dobrane uszczelnienia skutecznie minimalizują ryzyko utraty płynów roboczych, co nie tylko sprzyja ochronie środowiska, ale także pozwala na obniżenie kosztów związanych z koniecznością uzupełniania tych substancji. W ten sposób organizacje unikają dodatkowych wydatków oraz potencjalnych problemów prawnych związanych z zanieczyszczeniem.
Wydłużenie żywotności komponentów to kolejny ważny atut stosowania uszczelnień hydraulicznych. Starannie dobrane materiały oraz odpowiednia konstrukcja tych uszczelnień ograniczają zużycie części mechanicznych, co przekłada się na mniejsze przestoje i niższe koszty konserwacji urządzeń. Jakość używanych materiałów ma również znaczenie w kontekście odporności na wysokie ciśnienia oraz różnorodne chemikalia, co jest szczególnie istotne w trudnych warunkach pracy.
Wszystkie te korzyści – od zwiększonej efektywności systemów hydraulicznych po ochronę przed wyciekami i dłuższą żywotność komponentów – przyczyniają się do poprawy funkcjonalności i niezawodności maszyn w wielu gałęziach przemysłowych.
Zwiększenie efektywności systemów hydraulicznych
Uszczelnienia hydrauliczne mają fundamentalne znaczenie w funkcjonowaniu systemów hydraulicznych, gdyż wpływają na ich wydajność. Odpowiedni dobór i zastosowanie tych elementów pozwala na znaczne ograniczenie strat energii, co przekłada się na lepszą efektywność całej instalacji.
Wzrost wydajności osiąga się dzięki:
- eliminacji wycieków,
- redukcji tarcia pomiędzy ruchomymi częściami,
- ochronie przed niepożądanym wypływem cieczy,
- stabilizacji ciśnienia wewnętrznego.
- przedłużeniu żywotności poszczególnych komponentów.
Utrzymanie stabilnego ciśnienia jest niezwykle istotne dla prawidłowego działania maszyn. Co więcej, odpowiednio dobrane uszczelnienia mogą znacznie obniżyć koszty eksploatacji całego systemu. Dlatego podczas projektowania i wdrażania systemów hydraulicznych kluczowe jest zwrócenie uwagi na jakość oraz rodzaj stosowanych uszczelnień. Taki wybór przyczynia się do zwiększenia efektywności ich działania.
Ochrona przed wyciekami
Ochrona przed wyciekami to fundamentalna rola, jaką pełnią uszczelnienia hydrauliczne. Te kluczowe elementy w systemach hydraulicznych zapobiegają niekontrolowanemu wydostawaniu się płynów roboczych, co mogłoby prowadzić do poważnych awarii oraz strat finansowych. Odpowiednio dobrane uszczelnienia nie tylko zabezpieczają system przed zanieczyszczeniami, ale także podnoszą jego efektywność.
Uszczelnienia hydrauliczne, wykonane z wysokiej jakości materiałów jak guma czy PTFE (teflon), wyróżniają się dużą odpornością na ciśnienie i temperaturę. Ważne jest jednak ich precyzyjne dopasowanie do konkretnego zastosowania, aby zapewnić szczelność. Niewłaściwy wybór może skutkować poważnymi problemami w funkcjonowaniu całego układu. Dlatego analizowanie wymagań projektowych przy wyborze odpowiednich uszczelniaczy ma kluczowe znaczenie.
Wydajne uszczelnienia nie tylko chronią przed wyciekami, ale również przyczyniają się do zwiększenia trwałości całego systemu hydraulicznego. Regularne monitorowanie stanu tych elementów oraz ich wymiana w razie potrzeby są niezbędne dla utrzymania sprawności maszyn i urządzeń.
Wydłużenie żywotności komponentów
Wydłużenie żywotności elementów systemów hydraulicznych odgrywa kluczową rolę w zapewnieniu ich efektywności oraz obniżeniu kosztów eksploatacji. W tym kontekście wysokiej jakości uszczelnienia hydrauliczne mają ogromne znaczenie. Skuteczne uszczelnienia znacznie redukują zużycie komponentów, co sprawia, że naprawy i wymiany są rzadziej konieczne.
Uszczelnienia te skutecznie chronią przed wyciekami oleju i innymi płynami roboczymi, co przekłada się na lepszą wydajność całego systemu oraz mniejsze ryzyko awarii. Utrzymanie odpowiedniego ciśnienia i temperatury pracy staje się możliwe dzięki zastosowaniu materiałów o wysokich parametrach, takich jak:
- guma,
- PTFE (teflon).
Inwestując w odpowiednie uszczelnienia hydrauliczne, zyskujemy nie tylko poprawę funkcjonalności systemu, ale także długofalowe oszczędności związane z ograniczeniem liczby napraw i wymian komponentów.
Jakie są najczęstsze błędy przy wyborze uszczelnień hydraulicznych?
Wybór uszczelnień hydraulicznych bywa niełatwym zadaniem, a wiele osób popełnia przy tym znaczące błędy. Oto najczęstsze z nich:
- ignorowanie specyfikacji technicznych,
- niedostateczne zrozumienie wymagań związanych z ciśnieniem roboczym, temperaturą oraz środowiskiem chemicznym,
- złe dopasowanie surowców,
- wybór uszczelnień hydraulicznych z niewłaściwych tworzyw,
- brak testów przed montażem.
Niezrozumienie wymagań może prowadzić do zastosowania niewłaściwych materiałów, co z kolei naraża nas na szybkie zużycie lub nawet awarie całego systemu. Dlatego tak istotna jest dokładna analiza właściwości materiałów przed podjęciem decyzji.
Przed instalacją warto przeprowadzić odpowiednie próby, aby upewnić się, że spełniają one wymagania i są w stanie sprostać warunkom eksploatacyjnym.
Unikanie tych pułapek jest kluczowe dla prawidłowego funkcjonowania systemów hydraulicznych i pozwala jednocześnie ograniczyć ryzyko wycieków oraz awarii.
Ignorowanie specyfikacji technicznych
Ignorowanie specyfikacji technicznych podczas wyboru uszczelnień hydraulicznych może prowadzić do poważnych konsekwencji. Odpowiednie uszczelnienia odgrywają kluczową rolę w prawidłowym funkcjonowaniu systemów hydraulicznych, a ich niewłaściwy wybór często skutkuje awariami, co wiąże się z wysokimi kosztami napraw.
Specyfikacje techniczne uwzględniają wiele aspektów, takich jak:
- ciśnienie robocze,
- temperatura pracy,
- warunki chemiczne.
Nieprzestrzeganie tych norm zwiększa ryzyko wycieków i może znacznie skrócić żywotność poszczególnych komponentów. Dlatego tak ważne jest, aby uszczelnienia hydrauliczne były dobierane zgodnie z wymaganiami projektowymi, co zapewnia ich efektywność oraz niezawodność.
Z tego względu warto dokładnie zapoznać się ze wszystkimi parametrami technicznymi przed dokonaniem zakupu. Konsultacja z ekspertami oraz przeprowadzanie testów przed zastosowaniem to istotne kroki, które mogą pomóc w uniknięciu błędów przy doborze odpowiednich uszczelnień hydraulicznych.
Niewłaściwe dopasowanie materiałów
Niewłaściwy dobór materiałów do uszczelnień hydraulicznych to jeden z najczęstszych problemów, z jakimi można się spotkać. Taki błąd może prowadzić do szybkiego zużycia i obniżonej efektywności uszczelnień. Każdy materiał charakteryzuje się unikalnymi właściwościami, które muszą być dostosowane do specyficznych wymagań danej aplikacji.
Na przykład:
- guma nie sprawdzi się w wysokotemperaturowych warunkach ani w obecności agresywnych substancji chemicznych,
- PTFE, znany jako teflon, wyróżnia się doskonałą odpornością chemiczną i jest idealny w trudnych okolicznościach,
- metalowe uszczelnienia są bardziej wytrzymałe i odporne na ekstremalne warunki, ale często wymagają dodatkowych powłok ochronnych dla zachowania swojej efektywności.
W procesie wyboru materiałów do produkcji uszczelnień hydraulicznych należy uwzględnić takie czynniki jak ciśnienie robocze oraz temperatura pracy systemu. Niewłaściwe dopasowanie tych elementów może prowadzić do awarii systemu hydraulicznego, co wiąże się z kosztownymi naprawami oraz przestojami w pracy. Dlatego przeprowadzanie dokładnych analiz i testów przed wdrożeniem konkretnych rozwiązań jest kluczowe dla zapewnienia sprawności całego systemu.
Brak testów przed zastosowaniem
Brak przeprowadzania testów przed zastosowaniem uszczelnień hydraulicznych może skutkować poważnymi problemami z działaniem całego systemu. Testowanie tych elementów jest niezwykle istotne, ponieważ pozwala na wykrycie potencjalnych wad w materiałach i ich konstrukcji. Gdy ten proces zostaje pominięty, zwiększa się ryzyko wystąpienia:
- wycieków,
- awarii mechanicznych,
- spadku efektywności systemu.
Odpowiednio przeprowadzone testy umożliwiają dokładną ocenę trwałości uszczelnień hydraulicznych w różnych warunkach eksploatacyjnych. W przypadku braku takich badań, istnieje realne zagrożenie, że uszczelnienia nie będą w stanie sprostać wymaganiom związanym z ciśnieniem roboczym lub temperaturą. To z kolei ma negatywny wpływ na funkcjonowanie całej instalacji hydraulicznej.
Ważne jest, aby testowanie obejmowało:
- symulacje rzeczywistych warunków pracy,
- długoterminowe obserwacje zachowania materiału,
- wpływ różnych czynników chemicznych i mechanicznych.
Dlatego warto zainwestować czas w kompleksowe próby przed wdrożeniem uszczelnień hydraulicznych do codziennego użytku.